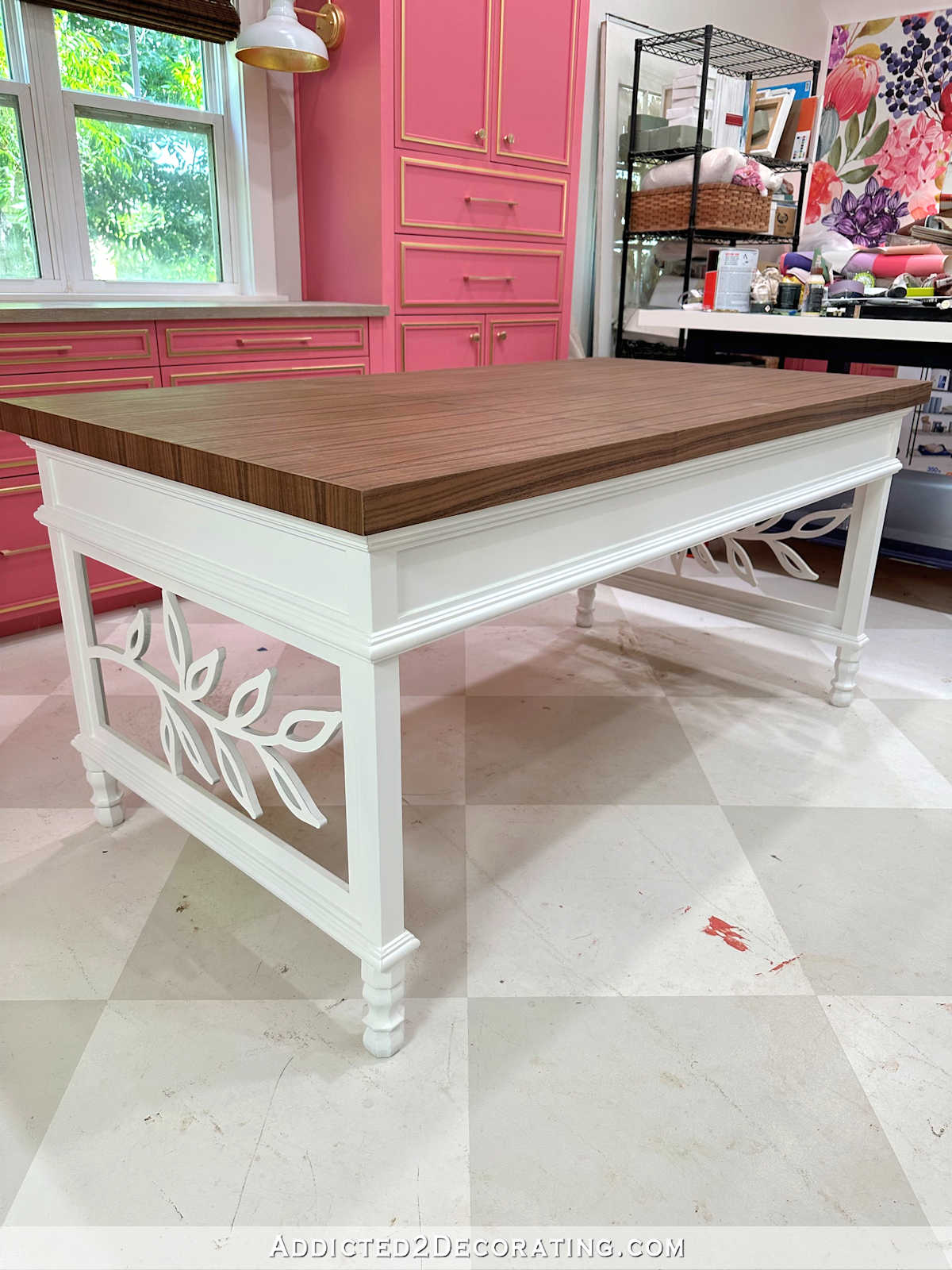
My studio desk is completed! I had initially deliberate a fast and simple desk makeover, however ultimately, I principally ended up rebuilding the desk. I constructed the unique desk a couple of years in the past. For some motive, I assumed I wished a really primary, trendy desk. It had a black base and a darkish stained prime. However the desk didn’t look proper within the studio, the place I used to be making a degree to make issues lighter, brighter, and extra female. So I got down to flip the unique desk into one thing extra becoming for my studio.
Right here’s a have a look at how the desk sorted I constructed it a couple of years again…
And right here’s what the desk seems like now…

In my final put up on this challenge, I had completed the desk base. As soon as it was all painted one shade, it seemed like this…

The following step was to complete the desktop. The unique desktop was the identical dimensions as the bottom. That gave it a contemporary look. However on this model, I wished the desktop to increase previous the bottom to provide it a extra conventional look. I didn’t wish to begin from scratch, although. The unique desktop was a strong core door, which was very heavy and sturdy. I wished to make use of it, however I wanted so as to add to the perimeters earlier than gluing on the veneer.
So I lower strips of 1-inch lumber, ripped to the proper width utilizing my desk noticed in order that these strips would cowl the sting of the desktop. After which I nailed these strips onto the perimeters of the desktop utilizing 16-gauge, 1.5-inch nails.

Right here’s what it seemed like with the strips connected to all 4 sides…

Since all of this could be hidden beneath veneer, there wasn’t any have to miter the corners…

However only one strip wasn’t sufficient. That solely prolonged all sides an extra 3/4-inch, and I wanted double that. So I added a second strip to every aspect…

Once more, I didn’t hassle mitering the corners. However I did use my sander to ensure the corners the place the boards met had been very clean.

Right here’s what it seemed like with two strips connected to all 4 edges.

Subsequent, I gave the highest a fast sanding with 100-grit sanding discs, not solely to take away the paint and glue that had been on the desktop, but in addition to ensure the transition from the unique desktop to the newly connected strips on the perimeters was very clean with no excessive spots.

Then I used to be prepared to connect the veneer. I used a 4′ x 8′ sheet of quartered walnut veneer for this desktop. I began by inserting the sheet flat, after which slicing off a 2.25-inch strip from the proper finish of the veneer. This piece could be for the proper edge, however I didn’t wish to connect it simply but.

Subsequent, I lower off a 2.25-inch strip on the entrance fringe of the veneer. That is the piece I glued on first. I connected the veneer utilizing Weldwood Contact Cement and a 6-inch curler for clean surfaces. I at all times put two coats of contact cement on each surfaces (the again of the veneer and the sting of the desk on this case), letting it dry utterly between coats, after which letting it dry utterly earlier than attaching the veneer. I connected the strip of veneer in order that it caught up above the desktop about 1/4-inch. Not less than, that was the aim. It wasn’t excellent. As soon as it was connected, I used a ground curler to ensure it was securely connected, after which used a utility knife with a model new blade to chop off the surplus 1/4-inch (or extra) from the highest fringe of the veneer.

The following piece that I connected was the highest. After coating each surfaces with two coats of contact cement and letting it dry, I positioned strips of scrap wooden on the desktop about six inches aside, spanning the entire desktop, after which positioned the veneer on prime. These strips saved the veneer from touching the desktop earlier than I used to be prepared. I lined up the proper edge and the entrance edge in order that the veneer overlapped about 1/4-inch, after which pressed the veneer into place from proper to left, eradicating one strip of wooden at a time and urgent the veneer into place. After which I used my utility knife to trim the proper edge and the entrance edge.

The again edge and the left edge had a complete lot of overlap. I wanted to watch out in slicing off this extra as a result of, as a lot as I may, I wished to scale back waste in order that I may get the grain on the perimeters to line up with the highest as a lot as potential. And if I lower away an excessive amount of, and had an excessive amount of scrap between the items, the grain wouldn’t line up.

I ended up dropping about 1/2 inch of veneer between the 2 items as soon as I rigorously lower off the surplus after which trimmed each…

You may see right here that after I lower off the massive piece of extra veneer from the left aspect, trimmed the veneer on the desktop, after which connected the veneer to the left edge, the grain nonetheless matched up fairly properly, regardless that I misplaced about 1/2-inch of veneer in that course of.

Additionally, sanding makes all of the distinction in the case of working with veneer. That is one motive I really like working with actual wooden veneer. For instance proper after attaching the veneer to the left aspect and trimming off the surplus from the highest edge, look how tough it seemed…

However after burnishing it down just a little extra, after which sanding that nook, that is the way it seemed…

After which as soon as I bought the surplus veneer trimmed off of the underside, that is how that left edge turned out…

And right here’s a have a look at the completed prime, and the 2 completed edges (left edge and entrance edge), at that time…

Subsequent, I added the proper edge piece. This was the primary piece I lower from the massive piece of veneer, however I wanted to connect the highest earlier than including this edge. It’s so much simpler to match up a small piece to a big piece that’s already in place moderately than making an attempt to match up a big piece to a small piece that’s already in place.

After which lastly, I connected the again edge (i.e., the desk chair aspect).

And right here’s the way it seemed as soon as all the pieces was trimmed and sanded.

And right here’s a greater view of the desktop. Quartered veneer typically has fascinating patterns in it, and this piece had fairly a couple of. These don’t hassle me, however simply be aware that in the event that they do hassle you, and also you’re wanting to make use of veneer on a challenge, you would possibly wish to search for a special lower of veneer.

To seal the desktop, I used the identical product that I used on the entire walnut in our rest room — Rubio Monocoat Oil Plus 2C in Pure (affiliate hyperlink). These things is AMAZING. It’s an oil plus a hardener, and it’s extremely sturdy. All the walnut in our rest room seems simply pretty much as good right this moment because it did the day I completed it, and I’ve by no means needed to recoat.

After mixing the 2 elements collectively in a 1:3 hardener-to-oil ratio, I wiped it on with a paper towel. Simply be aware that that is NOT the right means to do that. It’s a lot simpler to use with one thing like a type of white spongy applicator issues that gained’t take in (and waste) quite a lot of oil, and that gained’t depart behind little bits of white within the oil. However I didn’t have a type of applicators, so I simply used a paper towel. It wasn’t ideally suited, however I made it work. Right here’s the distinction that the oil made within the shade…

I wiped oil onto the entire floor, let it set a couple of minutes, after which used a clear white rag to buff your complete floor. It leaves a beautiful matte end on the wooden.
And right here’s the oiled desktop. Isn’t that fairly?! I really like walnut. I simply love how deep and wealthy the colour is with out being too darkish.

Right here’s a comparability of the scrap piece of unfinished veneer on prime of the oiled veneer.

And with that, the desk was carried out.

I’m so happy with how this desk turned out. I really like being within the kitchen and looking out into the studio to see a glimpse of the desk, pendant mild, and pink cupboards. Now I simply want my purple velvet chair!

My mother came visiting yesterday, and when she noticed the desk with its new prime, she stated, “Wow! I knew it was going to be fairly, however I didn’t comprehend it was going to be THAT fairly!” 😀

I’ve to agree together with her. I knew it might be fairly, and I may make it work. However I believe the ultimate look far exceeded my expectations.

And I simply love sitting at this desk, with my arms resting on this clean wooden desktop, and looking out as much as see that stunning pendant mild. I’ll be spending many hours right here, and it’s simply excellent.

In any case was stated and carried out, I ended up not including drawers to the desk. I had one drawback after one other with that plan, so I ended up carrying the highest trim all the way in which throughout the again (chair aspect) of the desk, after which I wrapped the opposite trim round identical to I did on the underside beneath the leaf panel.

That offers it a completed search for now, whereas additionally permitting for the potential of including drawers later if I modify my thoughts.

Anyway, I’m so happy with how this turned out. I used to be very pleased with the unique desk for a few years. It was a very good, sturdy, helpful, utilitarian desk.

However I believe the brand new seems is so significantly better. It matches the studio so significantly better, and it’s rather more “me”.

In order that’s yet another huge challenge checked off of my “to do” checklist for this room. I’ve just some extra, together with some electrical work, some trim and door casings, and reupholstering my desk chair.

After which getting this room all cleaned up and arranged goes to be fairly the job. The considered tackling that job is just a little overwhelming proper now.

However at the very least this one is completed. And I’m simply so pleased with the way it turned out!

Addicted 2 Adorning is the place I share my DIY and adorning journey as I transform and enhance the 1948 fixer higher that my husband, Matt, and I purchased in 2013. Matt has M.S. and is unable to do bodily work, so I do the vast majority of the work on the home on my own. You can learn more about me here.
Trending Merchandise